2023.06.15
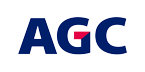
Leading the Industry through the Development of the “COCOA” Glass Melting Simulation Technology
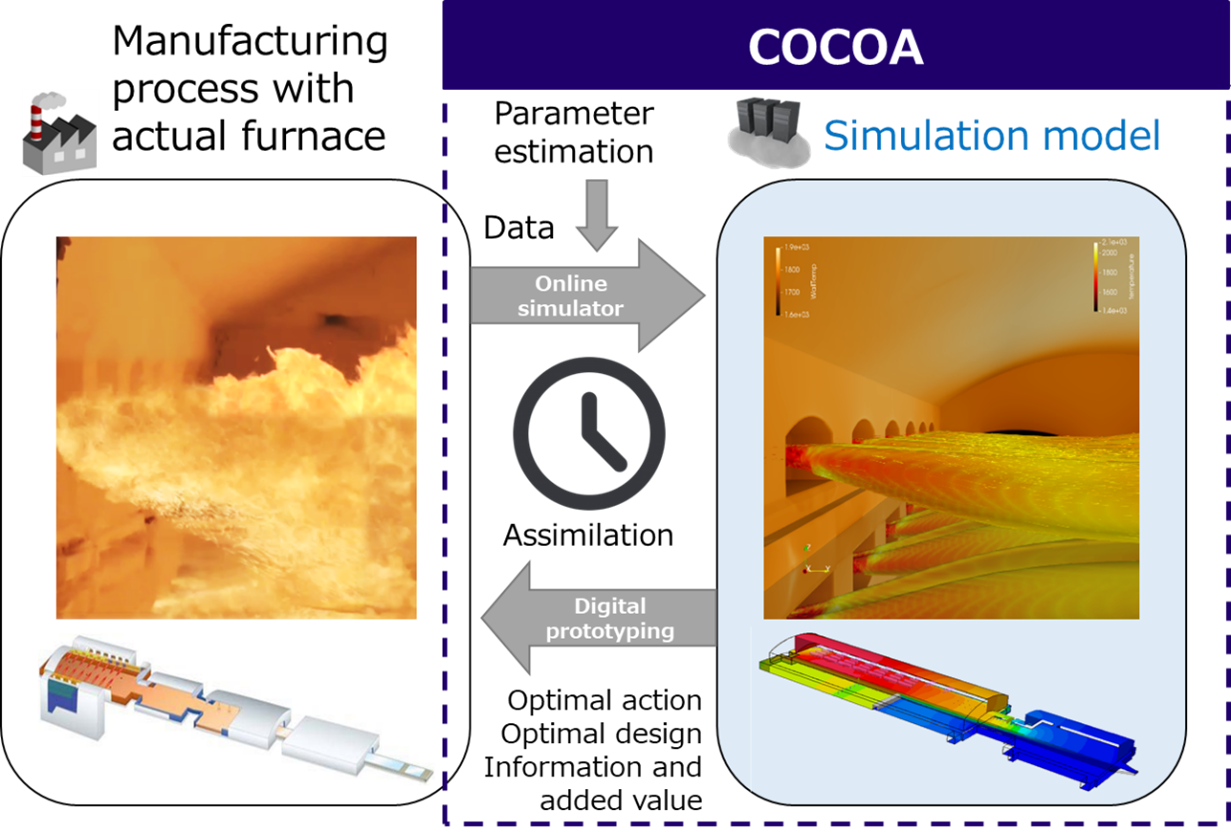
At facilities that produce flat glass using the float method, the manufacturing process is
conducted inside a float furnace, where the internal temperature reaches as high as 1600℃
and the entire production line can extend over a total length of 600 m to 1 km. Inside the
furnace, granular glass materials are melted into liquid, which is then floated and spread
thinly over melted tin to be processed into flat glass.
The internal temperature of a float furnace is so high that there are few components that
can withstand it. This makes it difficult to install a sensor in the furnace, which in turn
makes it very difficult to confirm the internal status, including the flow of the molten
glass, and check for bubbles and foreign matter. Moreover, because the manufacturing process
is implemented on an extremely large scale, if a problem occurs inside the furnace it is not
easy to identify the cause and find a solution. Even after you take action to deal with the
problem, it will take several days to a week just to get a response to that single action
from the equipment. During that period production will be suspended, resulting in extra
costs. To address this issue, AGC developed the “CADTANK” glass melting process simulation
technology independently in the 1970s and has been using it at its glass manufacturing
facilities as an indispensable technology.
Taiga Seki from the Hot Process Team at the Innovative Technology Laboratories’ Glass
Process Department has been engaging in development activities to update the simulation
technology.
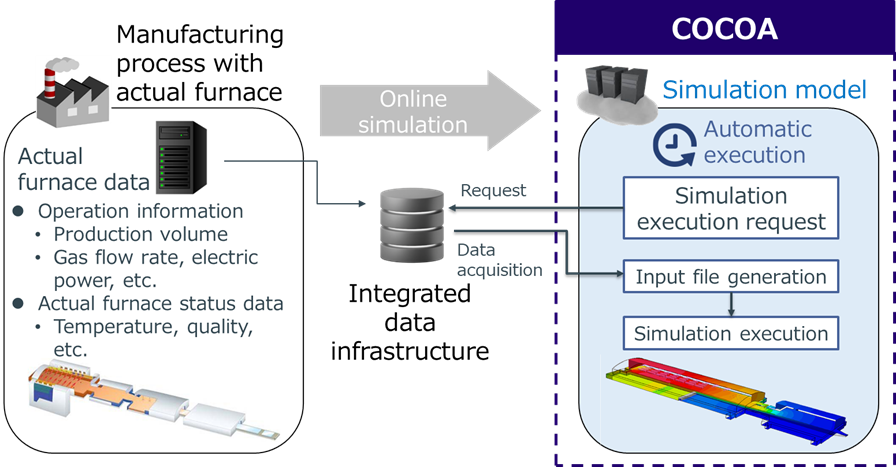
“In the conventional simulation model, a process technician sends an analysis request to an analysis expert, who then collects the actual furnace status data for simulation, carries out the simulation, and reports the results back to the technician,” explains Mr. Seki. “This workflow is time-consuming, and the fact that the number of analysis experts is limited also makes it difficult for a simulation to be carried out in a timely and detailed manner. In contrast, the newly developed CADTANK Online Computation and Optimization Assistant system automatically acquires actual furnace status data to reproduce the status synchronously in a virtual space by using digital twin technology. The system is designed to be a simulation tool that can easily be used by process technicians and even operators of actual furnaces who have no expertise in simulation.”
Fostering open innovation with Riken by applying weather forecasting technology
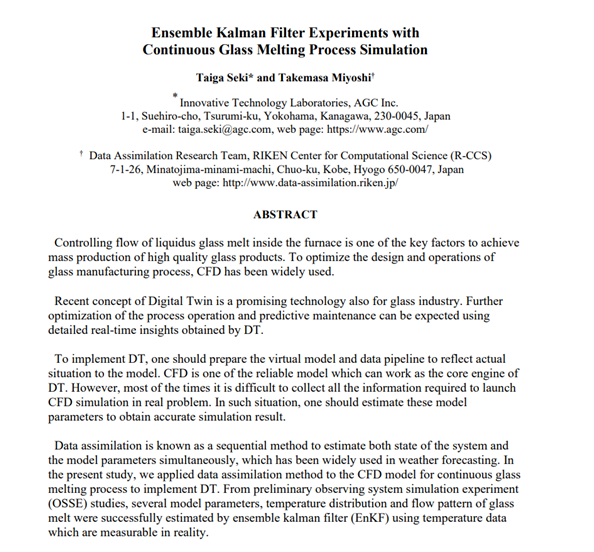
AGC started the operational verification of the CADTANK Online Computation and Optimization
Assistant (or “COCOA”), which is regarded as an epoch-making technology by the industry, in
February 2023. By automatically acquiring the actual furnace status data for online
simulation, COCOA makes it possible for manufacturing staff to check the internal situation
of the furnace in a timely and detailed manner. This will help them make improvements and
solve issues and will eventually lead to reductions in manufacturing cost and environmental
impact and to the solution of related issues.
“COCOA was built as a cloud-based system, but when I began to engage in the development
activities at the Innovative Technology Laboratories, there were few people at the
Laboratories who had ever used cloud technologies,” notes Mr. Seki. “Also, in order to make
it easier for on-site manufacturing staff to use the COCOA system, we have used the
programming language Python to turn the system into a web app, although we were initially
unfamiliar with Python. It was actually quite difficult for me to conduct the development
activities while learning two different types of new technologies, one related to cloud and
the other to Python.”
AGC has been producing glass for over 100 years but is still striving to improve. “We have
not yet reached the productivity that we aim for,” says Mr. Seki.
“Going forward,” he continues, “we need to meet the challenge of estimating the parameters.
For precise simulation, we need to collect a range of measurement information about the
actual furnace status. It is, however, difficult to carry out measurements inside the
furnace, and the kinds of data that can be collected automatically are still limited. As a
method for parameter estimation, we are looking at the data assimilation technology
developed in the field of weather forecasting. By applying this technology, we will be able
to automate the estimation, which is currently conducted by analysis experts through trial
and error, thereby further increasing simulation precision. Presently, we are promoting open
innovation with Dr. Takemasa Miyoshi, from the Data Assimilation Research Team at the RIKEN
Center for Computational Science. Dr. Miyoshi is a leading researcher in the field of data
assimilation.”
Mr. Seki first noted the significance of weather forecasting technology when he was
collecting information about simulation technologies in general and will continue to make
development efforts to keep improving COCOA.
INTERVIEWEE
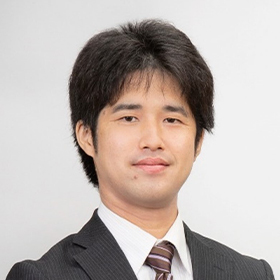
TAIGA SEKI
Hot Process Team, Glass Process Division, Innovative Technology Laboratories
AGC Inc.
1-5-1, Marunouchi, Chiyoda-ku, Tokyo
AGC was founded in 1907 and started business with the production of flat glass. The
company now conducts business in a range of fields including glass, electronics,
chemistry, life science and ceramics in more than 30 countries and regions.
Capitalizing on its world-class technologies, AGC provides materials and solutions
that are needed by society.